|
Knowledgebase
Blow Molding
Overview
Blowing
molding is the primary method to form hollow plastic objects
such as soda bottles, jerry cans, carboys. The process
includes clamping the ends of a softened tube of polymers
which can be either extruded or reheated, inflating the
polymer against the mold walls with a blow pin, and cooling
the product by conduction or evaporation of volatile fluids in
the container.
There are three general types of blow molding: extrusion blow
molding, injection blow molding, and stretch blow molding.
Extrusion blow molding is usually used to make items of weight
greater than 12 oz. such as containers for food, laundry, or
waste. Injection blow molding is used to achieve very accurate
wall thickness, high-quality neck finish, and to process
polymers that conot be extruded. Usual applications include
pharmaceutical, cosmetic, single serving liquor bottles that
weighs less than 12 oz. Stretch blow molding is only used for
difficult to blow crystalline and crystallizable polymers such
as polypropylene and polyethylene terephthalate.
Extrusion Blow Molding (parison)
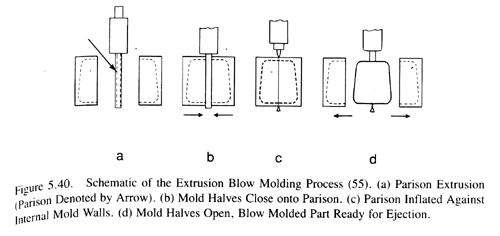
(a
parison is a plastic tubular form produced by extrusion
or injection molding)
This process usually use commodity materials such as PVC, PS,
PP, LDPE, HDPE. The extrusion part of the process is
continuous and the rest is cyclic. In order to get around the
problem, one can either do continuous parsion blow molding or
intermittent parison blow molding.
For continuous parsion blow molding, extrudate is produced
continuously which would achieve good melt uniformity. Several
molds will be used to process the extrudate. Swift parison
removal and control is required for this process.
For intermittent parison blow molding, the extra extruder must
either feed the melt into a separate ram accumulator or the
screw will reciprocate more waiting for the next batch. This
process is used for small scale production because it is not
as efficient as the continuous parison blow molding.
Important factors one should consider for extrusion blow
molding include the following:
* Polymer viscosity at high & low shear rates
* Melt strength (important for uniform wall thickness, no
holes)
* Strain recovery (MW & Distribution)
* Crystallization rate (slow rate desired)
* Thermal properties (thermal diffusitivity, thermal
conductivity, specific heat, etc.)
Injection Blow Molding
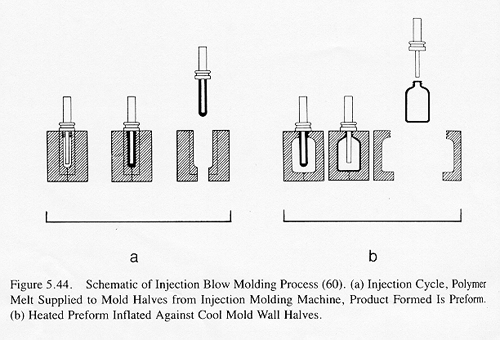
Injection blow molding include the following steps: at first,
the polymer is injection molded onto the core pin; then the
core pin is rotated to a blow molding station to be inflated
and cooled.
These factors are critical to this process:
* Shear & temperature dependent viscosity
* Temperature-dependent tensile strength on the pin
* Tensile elongation during inflation
* Crystallization kinetics on the core pin
* Crystallization kinetics during blowing and cooling
Stretch
Blow Molding (parison)
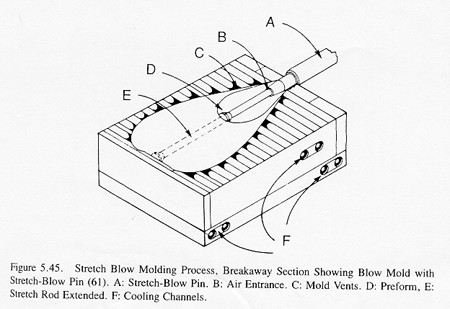
For Stretch Blow Molding, the
polymer is first heated to aboe the glass transition
temperature. Then polymer is inflated and stretched with a
hollow core-rod. This process resembles that of a rubber
balloon inflation.
Important polymer properties to be considered:
* Tensile strenth and yield above Tg
* Effect of orientation on gas permeability through the
polymer
Guide to Plastic Resins
High Density Polyethylene (HDPE)
is the most widely used resin for extrusion blown plastic
bottles. This material is economical, impact resistant, and
provides a good moisture barrier. HDPE is compatible with a
wide range of products including acids and caustics but is not
compatible with solvents. It is usually supplied in FDA
approved food grade. HDPE is naturally translucent and
flexible. The addition of color will make HDPE opaque although
not glossy. Adding extra weight to the bottle will yield a
rigid container. HDPE can be supplied electro-treated or
flame-treated by request so that it can be ready for silk
screen decoration. While HDPE provides good protection at
below freezing temperatures, it cannot be used with products
filled at over 180°F or products requiring a hermetic seal. A
glossy surface can be achieved with the use of the special
copolymer resin, High Gloss HDPE.
Post Consumer Resin (PCR) is a blend of reclaimed
natural HDPE (primarily from milk and water containers) and
virgin resin. The recycled material is cleaned, ground and
recompounded into uniform pellets along with prime virgin
material especially designed to build up environmental stress
crack resistance. PCR has no odor but exhibits a slight yellow
tint in its natural state. This tint can be hidden by the
addition of color. PCR is easily processed and inexpensive.
However, it cannot come into direct contact with food or
pharmaceutical products. PCR can be produced in a variety of
recycled content percentages up to 100%.
Low Density Polyethylene (LDPE) is similar to HDPE in
composition. It is less rigid and generally less chemically
resistant than HDPE, but is more translucent. LDPE is used
primarily for squeeze applications. LDPE is significantly more
expensive than HDPE, but will yield a glossy bottle when
produced in colors.
Medium Density Polyethylene (MDPE) combines the
characteristics of low and high density polyethylene. Bottles
are less translucent than LDPE but more flexible than HDPE.
Like LDPE, MDPE is glossy when produced in colors.
Polypropylene (PP) is a naturally translucent material
which provides contact clarity and an excellent moisture
barrier. PP is easily processed via injection molding (jars
and closures), and injection, extrusion, or stretch
blow-molding (bottles). One major advantage of polypropylene
is its stability at high temperatures, up to 200°F. Therefore,
it is used for hot fill products such as pancake syrup.
Polypropylene is also autoclavable and offers the potential
for steam sterilization. PP has excellent chemical resistance,
but provides poor impact resistance in cold temperatures.
Oriented PP offers improved impact resistance and clarity at
low temperatures. Produced in color, PP exhibits a glossy
finish.
K-Resin is ideally suited to a wide variety of
packaging applications by virtue of its sparkling clarity,
high gloss, and impact resistance.
K-Resin, a styrene derivative, is easily processed on
polyethylene equipment. It is suitable for packaging many
products but is specifically incompatible with fats and
unsaturated oils or solvents. This material is frequently used
for display and point-of-purchase packaging.
Polyvinyl Chloride (PVC) is naturally clear, has
extremely good resistance to oils, and has very low oxygen
transmission. It provides an excellent barrier to most gases
and its drop impact resistance is also very good. This
semi-rigid material is also very chemically resistant, but it
is vulnerable to solvents.
PVC is available in general purpose grade, food grade, and
fragrance-guard perfume grade. The occurrence of the blue tint
in clear PVC can be modified by controlling the toner levels
in each of these grades. General Purpose PVC will distort at
160°F, making it incompatible with hot filled products. New
PVC grades are able to withstand temperatures up to 190°F and
can be hot filled. Since it provides a good oxygen barrier,
PVC is an excellent choice for salad oil, mineral oil, and
vinegar. It is also commonly used for shampoos and cosmetic
products.
PETG is a durable material with excellent gloss,
clarity and sparkle desired for clear bottles. PETG can be
processed via conventional extrusion blow molding methods,
generally on machines designed to process PVC.
Applications include shampoos, soaps and detergents. PETG
exhibits a good impact strength and gas barrier. The chemical
resistance of PETG is fair and compatibility testing is
recommended, especially with products that contain alcohol.
Resin Chart
This chart is a useful guide
for performance of different materials, but is intended only
as a guideline. Being certain that a specific type of plastic
will serve all the needs of a specific product is a
complicated matter and may not be determined from this chart.
Resin |
Polyethylene
Terephthalate
PET |
Polyethylene PE
Low Density |
Polyethylene PE
High Density |
Polypropylene PP |
Resin Density |
1.35 |
0.91 to 0.925 |
0.94 to 0.965 |
0.89 to 0.91 |
Clarity |
Clear |
Hazy
Transparent |
Hazy
Transparent |
Moderate Hazy |
Moisture Barrier |
Fair to Good |
Good |
Good to Excellent |
Good to Excellent |
Oxygen Barrier |
Good |
Poor |
Poor |
Poor |
Acid Resistance |
Fair to Good |
Fair to Good |
Fair to Good |
Fair to Good |
Grease & Oil Resistance |
Good |
Good |
Good |
Good |
Distortion temperature |
125o to
160oF |
180o to
220oF |
175o to
180oF |
230o to
260oF |
Rigidity (stiffness) |
Moderate to High |
Low |
Moderate |
Moderate to High |
Impact Resistance |
Good to Excellent |
Excellent |
Good to Excellent |
Poor to Good |
Heat Resistance |
Poor to Fair |
Fair |
Good |
Good |
Cold Resistance |
Good |
Excellent |
Excellent |
Poor to Fair |
Sunlight Resistance |
Good |
Fair |
Fair |
Fair |
Resin |
Polystyrene PS |
Polyvinyl
Chloride
PVC |
Acrylonitrile Barex® |
Polyethylene
terephthalate
glycol PETG |
Resin Density |
1.0 to 1.1 |
1.35 |
1.15 |
1.27 |
Clarity |
Clear |
Clear |
Hazy
Transparent |
Clear |
Moisture Barrier |
Poor to Fair |
Fair |
Poor to Fair |
Fair |
Oxygen Barrier |
Good |
Good |
Good |
Good |
Acid Resistance |
Fair to Good |
Good to Excellent |
Good |
Fair |
Grease & Oil Resistance |
Fair to Good |
Good |
Good to Excellent |
Good |
Distortion temperature |
200o to
220oF |
140o to
150oF |
165o to
170oF |
140o to
160oF |
Rigidity (stiffness) |
Moderate to High |
Moderate to High |
Moderate to High |
Moderate to High |
Impact Resistance |
Poor to Good |
Fair to Good |
Poor to Good |
Good |
Heat Resistance |
Fair |
Poor to Fair |
Fair |
Fair |
Cold Resistance |
Poor |
Fair |
Fair to Good |
Good |
Sunlight Resistance |
Fair to Poor |
Poor to Good |
Fair |
Good |
|
 |